Automatic Backwash Filter
Background:
The filter is a device installed on the conveying medium pipeline so that the required fluid can pass through smoothly and the unwanted solid matter is trapped. It is usually installed on the pretreatment section of the material, including pressure relief valves, pressure relief valves, pneumatic control valves and other equipment.
Excessive impurities left in the filter make the filtration operation difficult and need to be cleaned in time. During cleaning, the filter cartridge or filter screen needs to be taken out, and then reloaded into the filter after cleaning. The entire cleaning operation is troublesome. Therefore, a backwash filter with no disassembly and cleaning was born, which can eliminate the original filter disassembly step and improve the work efficiency. Backwash filters are widely used in agriculture, electronics, medicine, dyes, petroleum, paper and other industries.
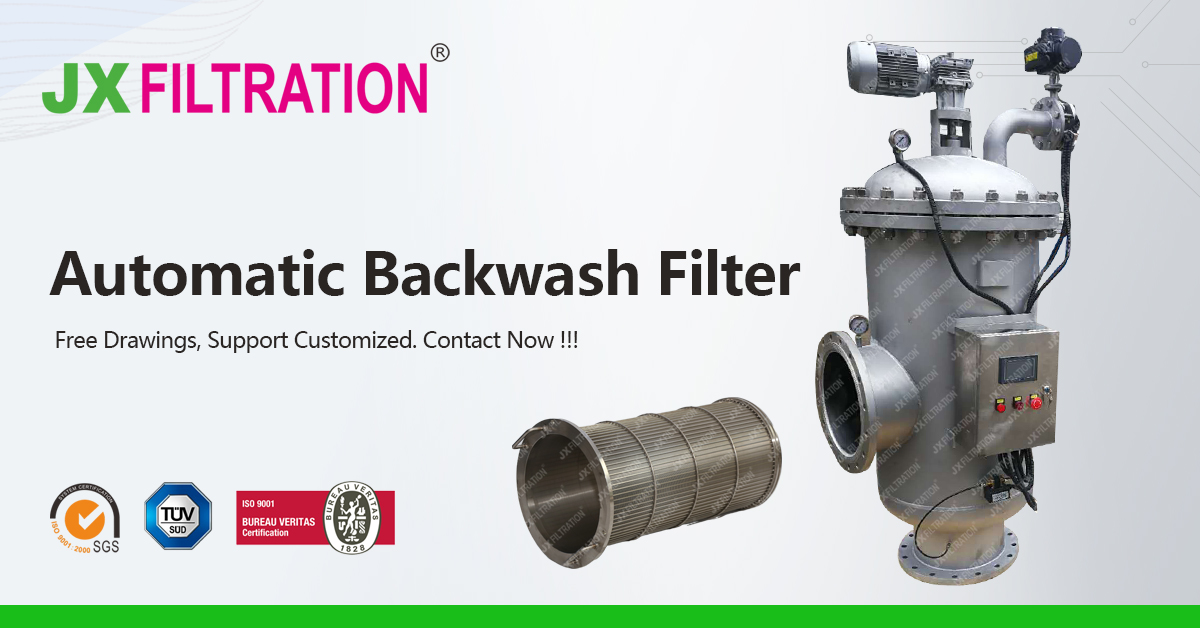
The backwash filter needs to increase the washing liquid inlet and cleaning automatic control device on the original filter design. When the pressure difference between the inlet and outlet of the filter reaches the specified value, the automatic cleaning system starts to clean the filter. Due to the access of the automatic control system, the cleaning accuracy is better controlled, and there is no outdated or early operation caused by manual operation, which improves the safety factor of production and reduces the difficulty of maintenance operations. Today's enterprises attach great importance to safety, and backwash filters can be installed in places that are difficult to reach or difficult to operate, which can reduce the incidence of safety accidents. When the filter is in normal use, the pressure difference on both sides will gradually increase with the increase of trapped particles. When the pressure difference reaches the set cleaning value, the material will be cut off, the cleaning motor will be started. The liquid port is injected to clean the filter element in the filter. After completion, the washing liquid is discharged from the sewage outlet. After the sewage discharge is completed, the washing liquid inlet valve and the washing liquid outlet valve are closed, and the material can pass normally, thus completing a cleaning cycle, and the cleaning time is generally controlled within 60 s.
There are generally two flushing methods:
(1) One-way timing flushing. The main material flows from left to right, and the pump used for the washing liquid is a centrifugal pump. When the washing condition is reached, the valve of the material pipeline is closed, the washing liquid outlet valve is opened, the motor is started, and then the washing liquid inlet valve is opened. The upper part of the filter element flushes the filter element downward, and the washed lotion flows out from the lower end of the filter and enters the lotion collection tank. This operation can be set in advance according to the cleaning needs. For example, the cleaning time of 5 minutes can clean the filter elements to meet the requirements. At this time, the cleaning time can be set to 5 minutes. After 5 minutes, the washing liquid inlet valve is closed, the motor is turned off, the washing liquid outlet valve is closed, the material inlet and outlet valves are opened, and the production continues. The above steps complete a backwashing operation.
(2) Circulating differential pressure control flushing. This flushing mode is based on the first one-way timing flushing mode, and its operation mode is also basically the same as the first one-way timing flushing mode. The difference between them is: the first flushing method is suitable for the flushing of insoluble solid particulate materials, and this flushing method is suitable for the conditions where the trapped impurities are all soluble. The first rinse mode lotion needs to be treated before it can be used. In this rinse mode, the lotion is used continuously. The flushing time is also determined according to the pressure difference between the two sides of the material, and the flushing is stopped after the pressure difference required by the process is reached. However, it should be noted that the flushing time should not be too long, otherwise the filter element should be replaced.
Any Requirements, Contact Us Now!
Nina
Email/Teams:nina@filtrationchina.com
Mobile/Whatsapp/Wechat: +86 17269571060
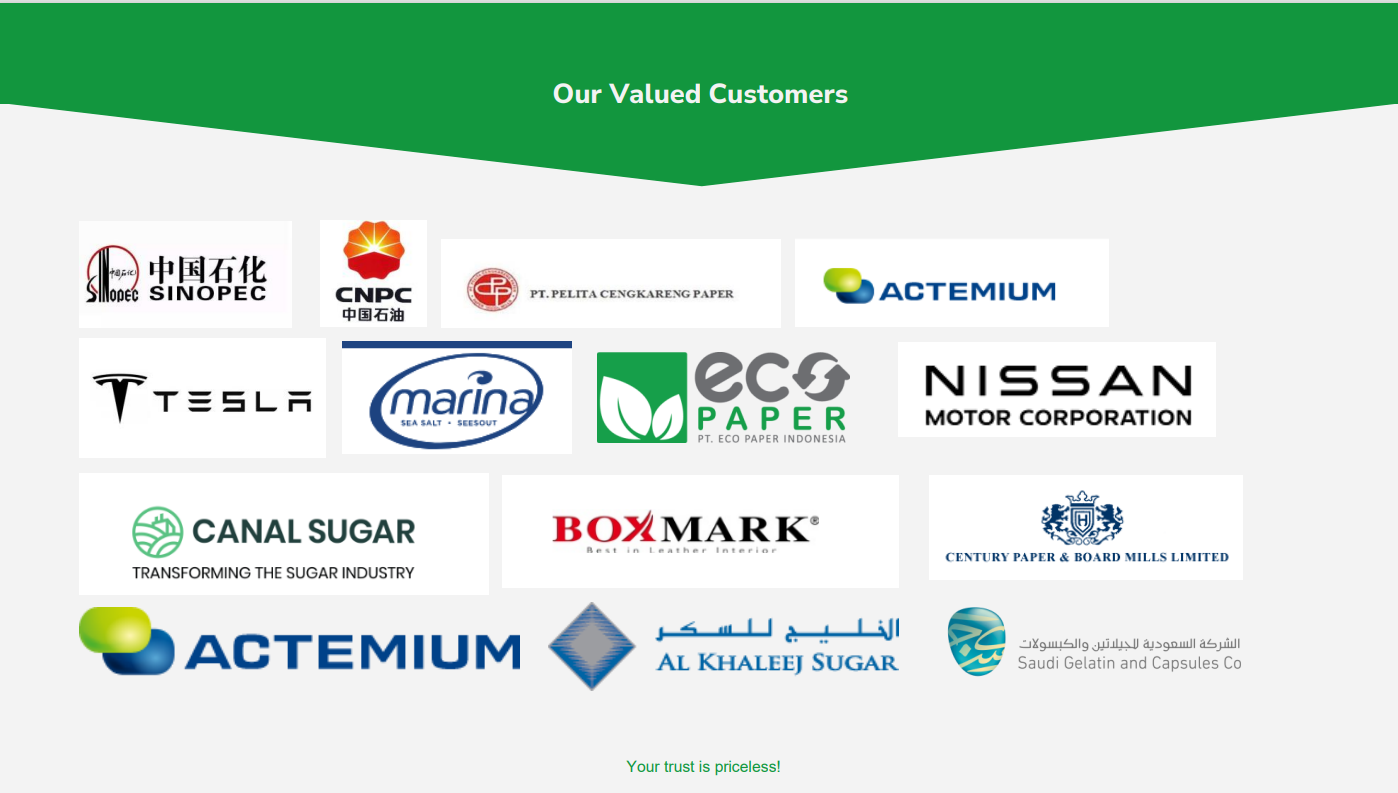